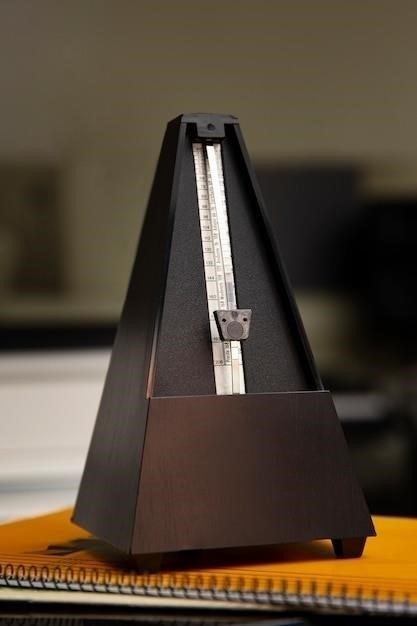
Millermatic 200 Manual⁚ A Comprehensive Guide
This comprehensive guide aims to provide you with a thorough understanding of the Millermatic 200 welding system․ Whether you’re a seasoned welder or a beginner, this manual will serve as your primary resource for operating, maintaining, and troubleshooting your Millermatic 200․ We’ll cover everything from key features and operational capabilities to safety precautions and troubleshooting tips․
Introduction
The Millermatic 200 is a versatile and reliable gas metal arc welding (GMAW) system that has been a staple in workshops and fabrication facilities for decades․ This manual is designed to provide you with a comprehensive understanding of this welding machine, empowering you to operate it effectively, safely, and efficiently․ We will delve into the intricacies of its features, operation, and maintenance, equipping you with the knowledge to maximize its performance and longevity․
The Millermatic 200, a product of Miller Electric Mfg․ Co․, has earned a reputation for its robust construction, ease of use, and consistent welding performance․ Whether you’re a seasoned welder or a newcomer to the world of GMAW, this manual will serve as your guide to unlocking the full potential of this welding machine․ We’ll cover everything from the basics of operation to advanced troubleshooting techniques, ensuring you have the resources to tackle any welding project with confidence․
This manual aims to be your one-stop resource for all things Millermatic 200․ It will provide you with the knowledge and skills necessary to use this welding machine effectively, safely, and with confidence․ By carefully reading through this manual, you’ll gain a deep understanding of its capabilities, limitations, and best practices for operation and maintenance․
Key Features of the Millermatic 200
The Millermatic 200 boasts a range of features designed to enhance your welding experience and deliver consistent, high-quality results․ Its compact design, weighing only 29 pounds (13․2 kg), makes it highly portable, allowing you to take your welding capabilities to any location․ The Millermatic 200’s versatility is further amplified by its ability to operate on both 120V and 230V power sources, providing flexibility for diverse welding environments․ This adaptability allows you to utilize the Millermatic 200 in both residential and industrial settings․
The Millermatic 200 comes equipped with a user-friendly control panel, making it easy to adjust settings and optimize welding parameters․ Its intuitive design enables you to fine-tune the welding process to suit different materials and applications, ensuring optimal results for your welding projects․ The Millermatic 200 also features a robust wire feed system, capable of handling a variety of wire diameters, providing you with the flexibility to choose the best wire for your specific welding needs․
The Millermatic 200’s durable construction ensures longevity and reliable performance, even in demanding environments․ Its solid build withstands the rigors of frequent use, making it a dependable companion for your welding tasks․ The Millermatic 200’s combination of portability, versatility, user-friendliness, and durability makes it an exceptional choice for both hobbyists and professionals seeking a reliable and efficient welding solution․
Operational Capabilities
The Millermatic 200 is a versatile welding machine capable of handling a wide range of welding tasks․ Its primary welding process is Gas Metal Arc Welding (GMAW), commonly known as MIG welding․ This process utilizes a continuous wire feed system, providing a smooth and consistent welding arc for efficient metal joining․ The Millermatic 200 is capable of welding various materials, including steel, aluminum, stainless steel, and other metals, making it suitable for a wide range of applications․
The Millermatic 200’s operational capabilities extend beyond MIG welding․ It can also be used for Stick welding, also known as Shielded Metal Arc Welding (SMAW), by utilizing the appropriate settings and accessories․ Stick welding is a versatile process that allows for welding in various positions and can be used for thicker materials and applications requiring a higher degree of precision․ The Millermatic 200’s ability to handle both MIG and Stick welding processes makes it a highly versatile tool for diverse welding needs․
The Millermatic 200’s wire feed system features a range of adjustable settings, allowing you to control the wire feed speed, voltage, and other parameters․ These adjustable settings enable you to fine-tune the welding process to suit different materials, thicknesses, and welding positions․ The Millermatic 200’s versatility in welding processes and adjustable settings make it a powerful tool for a wide range of welding projects․
Power Requirements
The Millermatic 200 is designed for both 120V and 230V power supply options, providing flexibility for diverse work environments․ When operating on a 120V circuit, the Millermatic 200 delivers a welding output of up to 120 amps, suitable for various welding tasks․ However, when connected to a 230V power source, the Millermatic 200’s output increases to 200 amps, significantly boosting its welding capacity and enabling it to handle larger and thicker materials․ This adaptability allows you to choose the appropriate power source based on your specific welding needs and available power supply․
The Millermatic 200’s power requirements are relatively modest for its welding capabilities․ Its compact size and lightweight design make it easily transportable to various locations․ This portability is further enhanced by its compatibility with both 120V and 230V power sources, allowing you to utilize the Millermatic 200 in a wider range of settings, including remote locations or areas with limited power access․ Whether you’re working on a small project in your garage or a larger construction site, the Millermatic 200’s power requirements and portability make it a convenient and efficient welding solution․
It’s crucial to ensure that your chosen power source meets the Millermatic 200’s specific requirements and provides adequate amperage for your intended welding applications․ Refer to the user manual for detailed information on power requirements and ensure that the electrical system is properly grounded for safe operation․
Welding Applications
The Millermatic 200 is a versatile welding machine capable of handling a wide array of welding applications, making it a valuable tool for both hobbyists and professionals․ Its robust design and reliable performance allow it to tackle various welding tasks, from simple repairs to intricate fabrication projects․ The Millermatic 200 excels in MIG welding, a process known for its speed, efficiency, and high-quality welds․ It’s commonly used for welding steel, stainless steel, aluminum, and other metals․
One of the key strengths of the Millermatic 200 is its ability to MIG weld up to 3/8″ thick materials in a single pass, particularly when operating on a 230V power source․ This capability streamlines the welding process and reduces the time required for completing projects․ Its versatility extends beyond MIG welding, as it can also be used for TIG and stick welding, further expanding its application range․ The Millermatic 200’s compatibility with different welding processes makes it a highly adaptable machine, suitable for a wide range of welding tasks․
Whether you’re welding thin sheet metal, thicker structural components, or intricate automotive parts, the Millermatic 200 provides the power and control needed to achieve high-quality welds․ Its user-friendly interface and intuitive controls allow both novice and experienced welders to operate the machine effectively, making it a suitable choice for diverse welding projects․ The Millermatic 200’s broad range of applications, combined with its reliable performance and ease of use, makes it a popular choice for welders across various industries and skill levels․
Maintenance and Troubleshooting
Regular maintenance is crucial for ensuring the longevity and optimal performance of your Millermatic 200․ By adhering to a consistent maintenance schedule, you can prevent potential issues and ensure that your welder operates smoothly․ The Millermatic 200 manual provides detailed instructions on how to perform routine maintenance tasks, including cleaning, lubrication, and inspecting components․ It’s recommended to clean the welding gun, wire feed system, and other parts regularly to prevent debris buildup that can affect performance․ Lubricating moving parts, like the wire feed drive motor, ensures smooth operation and reduces wear and tear․
In the event of encountering problems, troubleshooting is essential for identifying and resolving the issue efficiently․ The Millermatic 200 manual offers a comprehensive troubleshooting guide, covering a wide range of potential problems, including power issues, wire feed problems, and welding arc problems․ By carefully following the troubleshooting steps outlined in the manual, you can diagnose the root cause of the problem and implement the appropriate solution․
If you’re unable to resolve the issue using the troubleshooting guide, it’s advisable to contact a qualified technician for assistance․ Routine maintenance and effective troubleshooting are key to ensuring the reliable and long-lasting performance of your Millermatic 200, allowing you to tackle your welding projects with confidence․
Safety Precautions
Welding is an inherently dangerous process, and it’s paramount to prioritize safety while operating the Millermatic 200․ The manual emphasizes the importance of adhering to all safety precautions to minimize the risk of accidents and injuries․ Always wear appropriate personal protective equipment (PPE), including a welding helmet with a shade appropriate for the welding process, leather gloves, and fire-resistant clothing․ Ensure that the work area is well-ventilated to prevent the buildup of harmful fumes․ Keep flammable materials away from the welding area, and avoid working in enclosed spaces without adequate ventilation․
Before operating the Millermatic 200, inspect the welding cables, connectors, and ground clamp for any signs of damage․ Ensure that the welding circuit is properly grounded to prevent electrical shocks․ Never touch the welding electrode or the work piece while the arc is active․ If working in a confined space, use a respirator to protect against welding fumes․ Always maintain a safe distance from the welding arc to avoid burns․ When not in use, store the Millermatic 200 in a dry, well-ventilated area to prevent corrosion and damage․
By following these safety precautions and the instructions outlined in the Millermatic 200 manual, you can minimize the risk of accidents and injuries while maximizing your safety during welding operations․
Spool Gun Compatibility
The Millermatic 200 is compatible with a range of spool guns, which are specialized welding guns designed for feeding wire from a spool․ These guns are particularly useful for welding aluminum and other thin materials, as they provide greater control and accuracy over the wire feed rate․ The Millermatic 200 features a four-pin connector designed to accommodate a variety of spool guns, ensuring compatibility with a wide range of models․ The manual details the specific spool gun models that are compatible with the Millermatic 200, along with instructions on how to connect and operate them․
When choosing a spool gun for your Millermatic 200, consider factors such as the wire diameter you intend to use, the welding application, and the overall size and weight of the gun․ A lighter and more maneuverable gun may be preferable for delicate work, while a heavier-duty gun might be better suited for larger projects․ Always ensure that the spool gun is compatible with the Millermatic 200’s voltage and amperage ratings․ Properly connecting and configuring the spool gun is crucial for achieving optimal welding performance․ Refer to the Millermatic 200 manual for detailed instructions on connecting the spool gun, setting the wire feed rate, and adjusting other relevant parameters․
Manual Availability
Acquiring a copy of the Millermatic 200 manual is essential for understanding and operating your welding system effectively․ Fortunately, there are several avenues to access this valuable resource․ The most straightforward approach is to visit the official Miller Electric website, where you can download a digital copy of the manual in PDF format․ This option offers convenience and accessibility, allowing you to access the manual from any device with an internet connection․
Alternatively, you can explore online platforms dedicated to sharing technical manuals, such as ManualsLib․com․ These platforms often host a vast collection of manuals for various products, including the Millermatic 200․ While these online resources can be valuable, it’s crucial to ensure that the downloaded manual is authentic and corresponds to the specific model of your Millermatic 200․
If you prefer a physical copy of the manual, you can contact Miller Electric directly or visit authorized distributors․ They may have printed copies available for purchase or may be able to provide you with instructions on how to obtain one․ Having a readily available manual ensures you have access to vital information regarding safety precautions, operation procedures, troubleshooting tips, and maintenance recommendations․
Historical Context
The Millermatic 200 holds a significant place in the history of welding technology․ It was introduced by Miller Electric Manufacturing Company in the late 1970s and quickly gained popularity for its reliability, versatility, and user-friendly design․ This welding system emerged during a time when advancements in welding technology were rapidly transforming the industry․ The Millermatic 200 was a testament to Miller’s commitment to innovation and its dedication to providing welders with powerful and efficient tools․
The Millermatic 200 became a staple in various welding applications, from automotive repair to fabrication and construction․ Its compact size and portability made it a valuable asset for both professional welders and hobbyists․ This welding system played a crucial role in shaping the landscape of welding technology, paving the way for future advancements in welding equipment․ Its legacy continues to inspire and influence the design and development of welding systems today․
The Millermatic 200’s historical significance lies not only in its technological achievements but also in its impact on the welding industry․ It represented a turning point in the development of user-friendly and versatile welding systems, making welding more accessible and efficient for a wider range of users․ Its legacy continues to inspire and influence the development of welding systems today, solidifying its place as a true pioneer in the field of welding technology․
Technical Specifications
The Millermatic 200 boasts a robust set of technical specifications that contribute to its performance and versatility․ Understanding these specifications is crucial for optimizing your welding experience and ensuring safe operation․
One notable feature is its power source․ The Millermatic 200 can operate on both 120V and 230V power supplies, offering flexibility for various work environments․ This adaptability allows for use in both residential and industrial settings․ The Millermatic 200’s welding output ranges from 25 to 200 amps, providing ample power for a wide range of welding tasks․
The welding system’s compact size and lightweight design, weighing only 29 pounds, make it highly portable and easy to transport․ The Millermatic 200’s wire feed speed is adjustable, ranging from 50 to 500 inches per minute, providing precise control over the welding process․ This allows for tailored settings depending on the material being welded and the desired welding parameters․
The Millermatic 200’s duty cycle is 20% at 200 amps, indicating its ability to handle continuous welding for a specific duration before requiring a cool-down period․ This duty cycle is suitable for various applications, making it a reliable choice for both short and extended welding tasks․ The Millermatic 200’s technical specifications underscore its versatility and performance, making it a valuable asset for a wide range of welding needs․